

Incorrect washing and post-curing can result in dimensional or mechanical variation. Warping After Post-CureĪlways follow the recommended washing and curing procedures. Tip: A matte surface finish signifies a dry, clean part. Immediately dry the part with compressed air.Parts must be completely dry before post-curing.ĭry parts with compressed air followed by convection/static drying. Most wash times with IPA are between 2-3 minutes and never exceed 5 minutes. This warping may be immediately visible or it may develop over time. When parts are over-exposed to IPA, they absorb the IPA and swell, causing warping. Many ETEC materials are washed in 99% Isopropyl Alcohol (IPA). Always use the cleaning agent validated for your specific material.
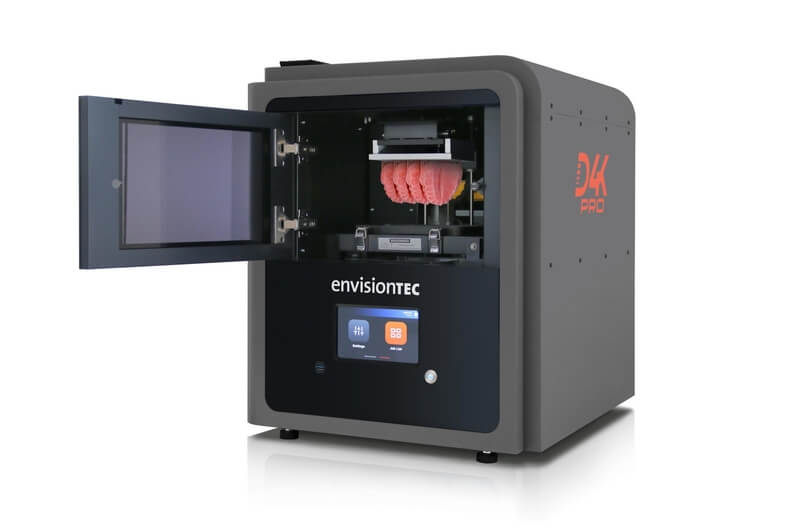
Warping During Wash CycleĪlways follow the recommended wash times during post-processing. Parts with overhangs or unsupported areas must have adequate supports to hold up the part. This reduces the risk of the new layer detaching from the previous layer, causing a print failure. When printing a heavy part, always use supports with thick contact tips. This setting is automatically applied in Envision One RP Software. Tip: The Burn-In adheres parts to the build platform by prolonging the initial exposures of the print job. However, the burn-in distorts the part by forming a lip across the bottom surface. Printing parts without support, directly on the build platform, provides a strong foundation. In a bottom-up 3D printer, parts are printed against gravity. Use Adequate SupportsĭLP 3D printing requires a strong foundation because each layer is built on top of the previous one.

If a part has a large flat surface parallel to the build platform, then the suction forces increase exponentially.Īngle the part by 10-20 degrees away from the build platform to reduce the surface area per layer. Parts are subject to suction force during the printing process. If the walls are thinner than the recommended size, consider redesigning the part in your CAD software. Wall thicknesses of 2.0 mm to 10.0 mm are printable without special considerations. The internal stresses from the resin's curing process can cause the parts to shrink and expand, leading to surface and internal cracks. Wall thickness is a major contributor to warping. If the internal stresses are not handled properly, part warping can occur. The transition from liquid to solid results in internal stresses. In DLP 3D printing, resin is cured by UV light. Printed parts can unintentionally warp, or curl, at different points in the 3D printing process:
